Destylator przemysłowy to urządzenie, które odgrywa kluczową rolę w wielu procesach produkcyjnych, zwłaszcza w przemyśle chemicznym i petrochemicznym. Jego głównym zadaniem jest separacja cieczy na podstawie różnic w temperaturze wrzenia składników. W praktyce oznacza to, że destylator może oddzielić substancje o różnych właściwościach fizycznych, co jest niezwykle istotne w produkcji czystych chemikaliów, alkoholi czy paliw. Proces destylacji odbywa się w kolumnie destylacyjnej, gdzie mieszanina cieczy podgrzewana jest do momentu, gdy jeden z jej składników zaczyna parować. Para następnie przemieszcza się w górę kolumny, gdzie schładza się i skrapla, a czysta substancja zbiera się na dnie kolumny. W zależności od zastosowanej technologii, destylatory mogą być jedno- lub wielostopniowe, co pozwala na uzyskanie wyższej czystości produktów końcowych.
Jakie są główne zastosowania destylatorów przemysłowych
Destylatory przemysłowe znajdują szerokie zastosowanie w różnych branżach, co czyni je niezwykle uniwersalnymi urządzeniami. W przemyśle chemicznym służą do produkcji rozmaitych substancji chemicznych, takich jak kwasy, zasady czy rozpuszczalniki. W branży spożywczej destylatory wykorzystywane są do produkcji alkoholi oraz olejków eterycznych. Na przykład, w procesie produkcji whisky czy wina destylacja jest kluczowym etapem, który wpływa na smak i jakość finalnego produktu. W przemyśle naftowym destylatory są niezbędne do rafinacji ropy naftowej, gdzie oddzielają różne frakcje paliwowe takie jak benzyna, olej napędowy czy nafta. Ponadto, destylatory znajdują zastosowanie w laboratoriach badawczych do oczyszczania substancji chemicznych oraz w procesach recyklingu, gdzie umożliwiają odzyskiwanie cennych surowców z odpadów.
Jakie są najważniejsze rodzaje destylatorów przemysłowych
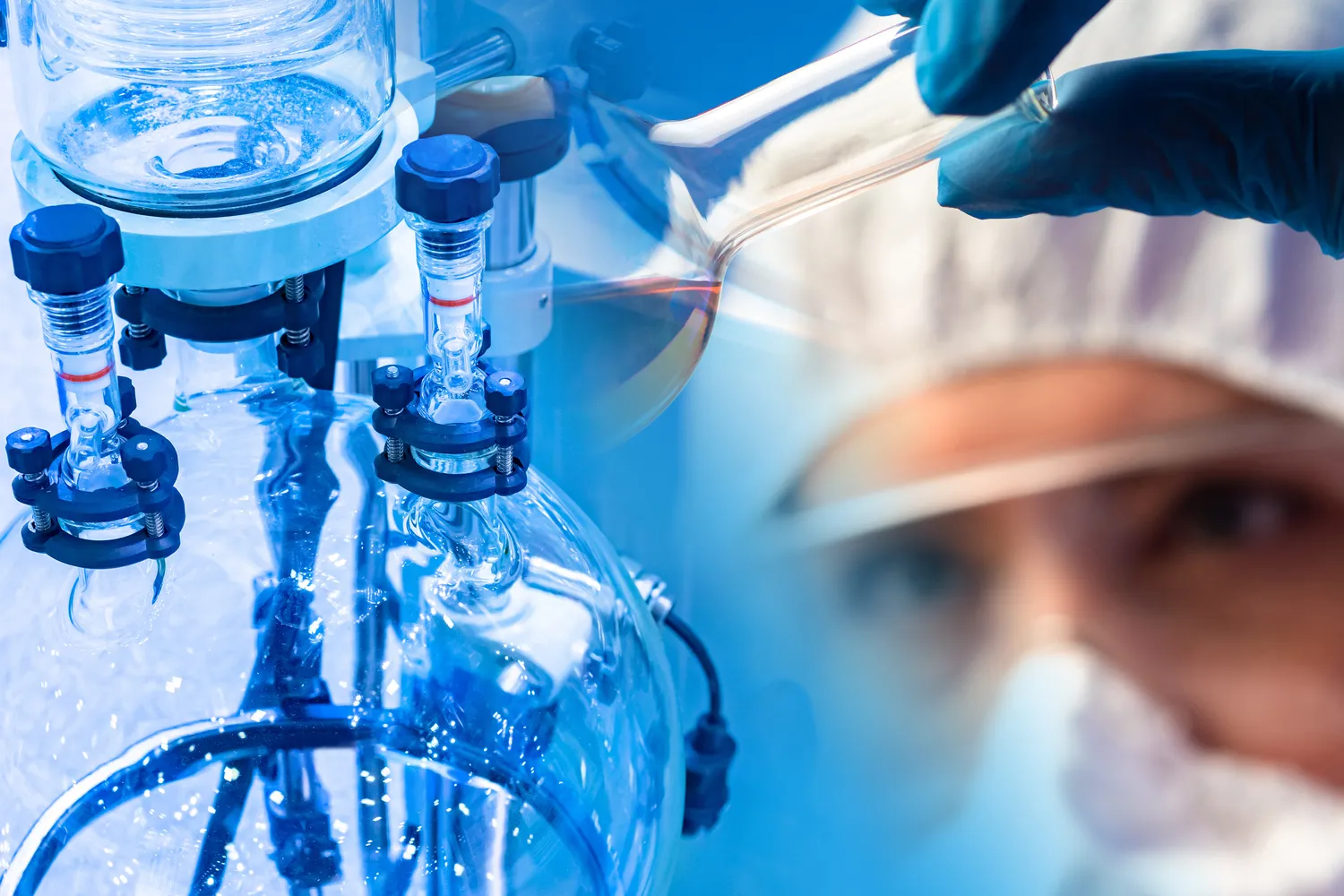
Wśród różnych typów destylatorów przemysłowych wyróżnia się kilka kluczowych rodzajów, które różnią się konstrukcją oraz sposobem działania. Destylatory prostokątne to najczęściej spotykany typ używany w przemyśle chemicznym i petrochemicznym. Charakteryzują się one prostą budową i są stosunkowo łatwe w obsłudze. Kolejnym popularnym rodzajem są destylatory kolumnowe, które umożliwiają przeprowadzanie wielostopniowej destylacji. Dzięki swojej konstrukcji pozwalają na uzyskanie wyższej czystości produktów końcowych oraz lepszą separację składników. Istnieją także destylatory próżniowe, które działają w obniżonym ciśnieniu, co pozwala na destylację substancji o wysokiej temperaturze wrzenia bez ryzyka ich degradacji. Warto również wspomnieć o destylatorach azeotropowych, które służą do separacji mieszanin azeotropowych – takich jak alkohol i woda – co jest szczególnie istotne w przemyśle spożywczym.
Jakie są kluczowe elementy budowy destylatora przemysłowego
Budowa destylatora przemysłowego opiera się na kilku kluczowych elementach, które współdziałają ze sobą podczas procesu destylacji. Najważniejszym z nich jest zbiornik grzewczy, który podgrzewa mieszaninę cieczy do momentu jej wrzenia. Zbiornik ten często wyposażony jest w systemy kontrolujące temperaturę oraz ciśnienie, co zapewnia optymalne warunki pracy. Kolejnym istotnym elementem jest kolumna destylacyjna, która pełni rolę miejsca separacji składników poprzez ich parowanie i skraplanie. Kolumna ta może być wyposażona w różnego rodzaju packingi lub tray’e, które zwiększają powierzchnię kontaktu między parą a cieczą oraz poprawiają efektywność procesu. Poza tym ważnym komponentem jest kondensator, który schładza parę i zamienia ją z powrotem w ciecz. Ostatnim kluczowym elementem jest zbiornik odbiorczy, gdzie gromadzi się produkt końcowy po zakończeniu procesu destylacji.
Jakie są najważniejsze zalety stosowania destylatorów przemysłowych
Stosowanie destylatorów przemysłowych niesie ze sobą szereg korzyści zarówno dla producentów, jak i dla jakości finalnych produktów. Przede wszystkim umożliwiają one uzyskanie wysokiej czystości substancji chemicznych poprzez skuteczną separację składników o różnych temperaturach wrzenia. Dzięki temu możliwe jest produkowanie chemikaliów o ściśle określonych parametrach jakościowych, co ma kluczowe znaczenie w wielu branżach takich jak farmaceutyka czy petrochemia. Kolejną zaletą jest możliwość automatyzacji procesów związanych z destylacją, co zwiększa efektywność produkcji oraz redukuje ryzyko błędów ludzkich. Nowoczesne urządzenia często wyposażone są w zaawansowane systemy monitorujące i kontrolujące procesy technologiczne, co pozwala na bieżąco dostosowywać parametry pracy do zmieniających się warunków. Dodatkowo stosowanie destylatorów przyczynia się do oszczędności energii dzięki możliwości recyklingu ciepła generowanego podczas procesu.
Jakie są najczęstsze problemy związane z destylatorami przemysłowymi
Podczas eksploatacji destylatorów przemysłowych mogą wystąpić różne problemy, które wpływają na efektywność i jakość procesu destylacji. Jednym z najczęstszych problemów jest tzw. flooding, czyli zjawisko zalewania kolumny destylacyjnej, które prowadzi do obniżenia efektywności separacji składników. Flooding może być spowodowane zbyt dużą ilością cieczy w kolumnie lub niewłaściwym doborem parametrów pracy, takich jak przepływ pary czy ciśnienie. Innym istotnym problemem jest tzw. weeping, które polega na niepożądanym przepływie cieczy przez tray’e kolumny, co również negatywnie wpływa na proces destylacji. Warto także zwrócić uwagę na kwestie związane z osadzaniem się zanieczyszczeń w kolumnie, co może prowadzić do spadku wydajności oraz konieczności przeprowadzania kosztownych czyszczeń. Problemy te mogą być minimalizowane poprzez regularne przeglądy techniczne oraz odpowiednie szkolenie personelu obsługującego urządzenia.
Jakie są nowoczesne technologie w dziedzinie destylacji przemysłowej
W ostatnich latach rozwój technologii w dziedzinie destylacji przemysłowej znacząco wpłynął na efektywność i jakość procesów produkcyjnych. Nowoczesne destylatory często wykorzystują zaawansowane systemy automatyzacji, które pozwalają na precyzyjne monitorowanie i kontrolowanie parametrów pracy. Dzięki zastosowaniu czujników temperatury, ciśnienia oraz przepływu możliwe jest bieżące dostosowywanie warunków pracy do zmieniających się potrzeb produkcji. Ponadto, coraz częściej stosuje się technologie membranowe oraz ekstrakcyjne jako alternatywy dla tradycyjnej destylacji, co pozwala na uzyskanie lepszej selektywności w separacji składników. Innowacyjne rozwiązania obejmują także zastosowanie nanotechnologii w budowie elementów kolumny destylacyjnej, co zwiększa powierzchnię kontaktu między parą a cieczą i poprawia efektywność procesu. Warto również wspomnieć o rosnącej popularności systemów odzysku ciepła, które pozwalają na oszczędność energii oraz redukcję kosztów operacyjnych.
Jakie są kluczowe czynniki wpływające na efektywność destylacji
Efektywność procesu destylacji zależy od wielu czynników, które należy uwzględnić podczas projektowania i eksploatacji destylatora przemysłowego. Przede wszystkim istotna jest temperatura wrzenia składników mieszanki – im większa różnica temperatur wrzenia, tym łatwiejsza separacja substancji. Kolejnym kluczowym czynnikiem jest ciśnienie panujące w kolumnie destylacyjnej; obniżenie ciśnienia może umożliwić destylację substancji o wysokiej temperaturze wrzenia bez ryzyka ich degradacji. Ważne jest także dobranie odpowiednich materiałów do budowy kolumny oraz elementów roboczych, które będą odporne na działanie chemikaliów i wysokich temperatur. Również konstrukcja samej kolumny ma znaczenie – zastosowanie odpowiednich packingu lub tray’ów zwiększa powierzchnię kontaktu między parą a cieczą, co przekłada się na lepszą efektywność separacji.
Jakie są wymagania dotyczące bezpieczeństwa w pracy z destylatorami przemysłowymi
Bezpieczeństwo pracy z destylatorami przemysłowymi jest niezwykle istotnym aspektem, który powinien być priorytetem dla każdego zakładu produkcyjnego. Przede wszystkim należy przestrzegać norm i przepisów dotyczących bezpieczeństwa chemicznego oraz ochrony środowiska. Wszyscy pracownicy powinni być odpowiednio przeszkoleni w zakresie obsługi urządzeń oraz procedur awaryjnych, aby móc szybko reagować w przypadku wystąpienia niebezpiecznych sytuacji. Ważnym elementem jest także regularne przeprowadzanie przeglądów technicznych oraz konserwacji urządzeń, co pozwala na wykrycie ewentualnych usterek przed ich eskalacją. Dodatkowo, zakład powinien być wyposażony w odpowiednie systemy wentylacyjne oraz detekcyjne, które umożliwiają monitorowanie stężenia szkodliwych substancji w powietrzu. Należy również zapewnić dostęp do sprzętu ochronnego dla pracowników, takiego jak maski ochronne czy rękawice chemiczne.
Jakie są przyszłe kierunki rozwoju technologii destylacyjnych
Przyszłość technologii destylacyjnych zapowiada się obiecująco dzięki dynamicznemu rozwojowi innowacyjnych rozwiązań oraz rosnącemu naciskowi na zrównoważony rozwój i efektywność energetyczną. W nadchodzących latach można spodziewać się dalszego wzrostu zastosowania technologii automatyzacji i cyfryzacji procesów produkcyjnych, co pozwoli na jeszcze dokładniejsze monitorowanie i kontrolę parametrów pracy destylatorów. Równocześnie rozwijane będą nowe materiały o lepszych właściwościach termicznych i chemicznych, które zwiększą wydajność procesów separacyjnych oraz ich trwałość. W kontekście ochrony środowiska coraz większą uwagę przykłada się do opracowywania technologii minimalizujących zużycie energii oraz emisję gazów cieplarnianych związanych z procesami produkcyjnymi. Można również oczekiwać dalszego rozwoju metod recyklingu ciepła oraz wykorzystania odnawialnych źródeł energii w procesach destylacyjnych.