Destylarka do rozpuszczalników to urządzenie, które wykorzystuje proces destylacji do oddzielania różnych substancji chemicznych na podstawie ich temperatury wrzenia. W praktyce oznacza to, że gdy mieszanka rozpuszczalników jest podgrzewana, substancje o niższej temperaturze wrzenia parują jako pierwsze, a następnie są skraplane i zbierane w osobnym pojemniku. Proces ten jest niezwykle efektywny, co sprawia, że destylarki są szeroko stosowane w laboratoriach chemicznych oraz w przemyśle. Warto zauważyć, że różne rozpuszczalniki mogą mieć zbliżone temperatury wrzenia, co wymaga precyzyjnego ustawienia parametrów destylacji. Użytkownicy muszą również zwracać uwagę na bezpieczeństwo podczas pracy z tymi urządzeniami, ponieważ niektóre rozpuszczalniki są łatwopalne lub toksyczne. Dlatego też odpowiednie wentylacje oraz środki ochrony osobistej są kluczowe dla zapewnienia bezpiecznego środowiska pracy.
Jakie są zalety używania destylarki do rozpuszczalników
Używanie destylarki do rozpuszczalników niesie ze sobą wiele korzyści, które przyciągają zarówno profesjonalistów, jak i amatorów zajmujących się chemią. Przede wszystkim, dzięki procesowi destylacji można uzyskać wysokiej czystości substancje chemiczne, co jest niezwykle istotne w wielu zastosowaniach laboratoryjnych i przemysłowych. Czystość uzyskanych produktów ma kluczowe znaczenie dla wyników eksperymentów oraz jakości produkcji. Kolejną zaletą jest możliwość recyklingu rozpuszczalników, co pozwala na oszczędność kosztów oraz zmniejszenie wpływu na środowisko. Dzięki temu można ponownie wykorzystać te same substancje w kolejnych procesach, co jest korzystne zarówno ekonomicznie, jak i ekologicznie. Dodatkowo nowoczesne destylarki często wyposażone są w zaawansowane systemy monitorowania i automatyzacji, co zwiększa komfort użytkowania oraz precyzję całego procesu.
Jakie rodzaje destylarek do rozpuszczalników są dostępne
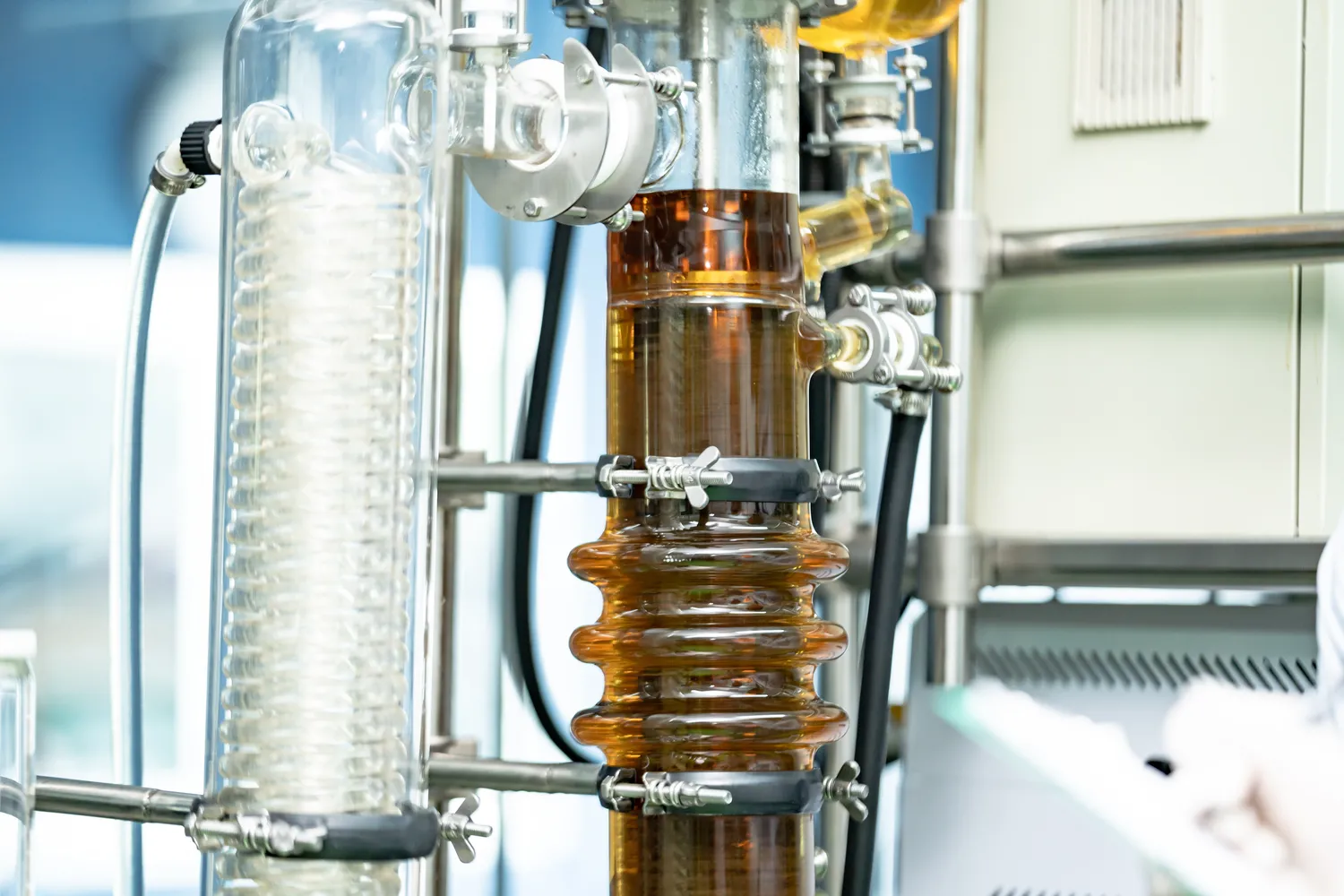
Na rynku dostępnych jest wiele różnych rodzajów destylarek do rozpuszczalników, które różnią się między sobą konstrukcją oraz przeznaczeniem. Najpopularniejsze z nich to destylarki prostokątne oraz okrągłe, które różnią się kształtem kolby oraz sposobem skraplania par. Destylarki prostokątne często wykorzystywane są w laboratoriach chemicznych ze względu na swoją efektywność w separacji substancji o zbliżonych temperaturach wrzenia. Z kolei destylarki okrągłe charakteryzują się większą powierzchnią skraplania, co może przyspieszyć proces oczyszczania. Istnieją również bardziej zaawansowane modele, takie jak destylarki frakcyjne, które pozwalają na oddzielanie wielu składników jednocześnie poprzez zastosowanie kolumny frakcyjnej. Tego typu urządzenia są szczególnie przydatne w przemyśle petrochemicznym oraz farmaceutycznym. Wybór odpowiedniej destylarki zależy od specyfiki pracy oraz wymagań dotyczących czystości końcowego produktu.
Jakie zastosowania mają destylarki do rozpuszczalników w przemyśle
Destylarki do rozpuszczalników znajdują szerokie zastosowanie w różnych gałęziach przemysłu, co czyni je niezwykle ważnym narzędziem dla wielu przedsiębiorstw. W przemyśle chemicznym służą one do oczyszczania surowców oraz produkcji wysokiej jakości substancji chemicznych, które są niezbędne w wielu procesach technologicznych. W branży farmaceutycznej destylacja odgrywa kluczową rolę w produkcji leków oraz ich składników aktywnych, gdzie czystość substancji ma fundamentalne znaczenie dla skuteczności terapeutycznej preparatów. Ponadto destylarki wykorzystywane są także w przemyśle kosmetycznym do produkcji perfum oraz innych kosmetyków zawierających różnorodne olejki eteryczne i ekstrakty roślinne. W sektorze spożywczym proces destylacji jest stosowany do produkcji alkoholi oraz aromatów naturalnych.
Jakie są najczęstsze problemy z destylarkami do rozpuszczalników
Podczas korzystania z destylarek do rozpuszczalników mogą wystąpić różnorodne problemy, które mogą wpłynąć na efektywność procesu oraz jakość uzyskiwanych produktów. Jednym z najczęstszych problemów jest nieprawidłowe ustawienie temperatury, co może prowadzić do niepełnej destylacji lub przegrzania substancji. W przypadku, gdy temperatura jest zbyt wysoka, może dojść do rozkładu chemicznego substancji, co skutkuje powstawaniem niepożądanych produktów ubocznych. Innym problemem jest zatykanie się kolumny frakcyjnej, co może być spowodowane osadzaniem się zanieczyszczeń lub niewłaściwym doborem materiałów. Zatykanie kolumny prowadzi do zmniejszenia efektywności destylacji i wydłużenia czasu procesu. Warto również zwrócić uwagę na kwestie związane z bezpieczeństwem, takie jak wycieki rozpuszczalników czy ich opary, które mogą być szkodliwe dla zdrowia.
Jakie materiały są używane do budowy destylarek do rozpuszczalników
Budowa destylarek do rozpuszczalników wymaga zastosowania odpowiednich materiałów, które zapewnią nie tylko efektywność procesu, ale także bezpieczeństwo użytkowania. Najczęściej wykorzystywanym materiałem jest szkło borokrzemowe, które charakteryzuje się wysoką odpornością na działanie chemikaliów oraz wysokie temperatury. Szkło borokrzemowe jest również łatwe do czyszczenia i nie wchodzi w reakcje z większością substancji chemicznych, co czyni je idealnym wyborem dla laboratoriów. W przypadku bardziej zaawansowanych modeli destylarek, takich jak destylarki frakcyjne, często stosuje się stal nierdzewną ze względu na jej wytrzymałość oraz odporność na korozję. Stal nierdzewna jest również łatwa w utrzymaniu czystości i może być stosowana w warunkach przemysłowych. Dodatkowo elementy uszczelniające wykonane są z materiałów odpornych na działanie wysokich temperatur oraz chemikaliów, co zapewnia szczelność układu i minimalizuje ryzyko wycieków.
Jakie są koszty zakupu destylarki do rozpuszczalników
Koszty zakupu destylarki do rozpuszczalników mogą się znacznie różnić w zależności od wielu czynników, takich jak typ urządzenia, jego pojemność oraz dodatkowe funkcje. Proste modele laboratoryjne można nabyć już za kilka tysięcy złotych, jednak bardziej zaawansowane urządzenia przemysłowe mogą kosztować nawet kilkadziesiąt tysięcy złotych. Warto również uwzględnić dodatkowe koszty związane z eksploatacją urządzenia, takie jak energia elektryczna potrzebna do podgrzewania substancji czy koszty konserwacji i napraw. Przy zakupie destylarki warto również zwrócić uwagę na producenta oraz dostępność części zamiennych, co może mieć wpływ na długoterminowe koszty użytkowania. Często inwestycja w droższe urządzenie o lepszej jakości może okazać się bardziej opłacalna w dłuższej perspektywie czasowej dzięki mniejszym kosztom eksploatacyjnym oraz większej niezawodności.
Jakie są różnice między destylarkami a innymi metodami oczyszczania
Destylacja to jedna z wielu metod oczyszczania substancji chemicznych, ale różni się od innych technik zarówno pod względem efektywności, jak i zastosowania. W porównaniu do filtracji, która polega na oddzieleniu ciał stałych od cieczy przy użyciu membran lub filtrów, destylacja pozwala na separację substancji na podstawie ich temperatury wrzenia. To sprawia, że proces ten jest znacznie bardziej skuteczny w przypadku mieszanin zawierających różne składniki chemiczne o różnych właściwościach fizycznych. Inną popularną metodą oczyszczania jest ekstrakcja rozpuszczalnikowa, która polega na wykorzystaniu rozpuszczalnika do wydobycia określonych składników z mieszanki. Choć ta metoda może być skuteczna w niektórych przypadkach, często wymaga użycia dużych ilości rozpuszczalników oraz może prowadzić do strat cennych substancji. Destylacja natomiast pozwala na odzyskanie praktycznie wszystkich składników mieszanki w formie czystej substancji chemicznej.
Jakie są nowinki technologiczne w dziedzinie destylacji
W ostatnich latach nastąpił znaczący rozwój technologii związanych z procesem destylacji, co przyczyniło się do zwiększenia efektywności oraz bezpieczeństwa pracy z destylarkami do rozpuszczalników. Nowoczesne urządzenia często wyposażone są w zaawansowane systemy automatyzacji, które umożliwiają precyzyjne monitorowanie parametrów pracy oraz automatyczne dostosowywanie ich w czasie rzeczywistym. Dzięki temu użytkownicy mogą osiągnąć optymalne wyniki bez konieczności ciągłego nadzorowania procesu. Ponadto rozwój technologii materiałowych pozwolił na produkcję komponentów odpornych na działanie wysokich temperatur oraz agresywnych substancji chemicznych, co zwiększa trwałość i niezawodność urządzeń. Innowacje obejmują także zastosowanie sztucznej inteligencji i uczenia maszynowego w celu optymalizacji procesów produkcyjnych oraz przewidywania potencjalnych problemów związanych z pracą destylarki.
Jakie są najlepsze praktyki dotyczące użytkowania destylarki do rozpuszczalników
Aby zapewnić prawidłowe działanie destylarki do rozpuszczalników oraz maksymalizować jej efektywność, warto przestrzegać kilku najlepszych praktyk dotyczących jej użytkowania. Przede wszystkim należy dokładnie zapoznać się z instrukcją obsługi dostarczoną przez producenta i stosować się do zaleceń dotyczących ustawień temperatury oraz ciśnienia roboczego. Regularne czyszczenie elementów urządzenia jest kluczowe dla utrzymania jego wydajności – osady chemiczne mogą prowadzić do obniżenia efektywności procesu destylacji oraz zwiększać ryzyko awarii. Ważne jest także monitorowanie jakości surowców wykorzystywanych w procesie – ich czystość ma bezpośredni wpływ na jakość końcowego produktu. Użytkownicy powinni również dbać o odpowiednią wentylację pomieszczenia, w którym znajduje się destylarka, aby uniknąć gromadzenia się szkodliwych oparów rozpuszczalników.
Jakie są przyszłe kierunki rozwoju technologii destylacji
Przyszłość technologii destylacji zapowiada się obiecująco dzięki ciągłemu postępowi naukowemu oraz rosnącym wymaganiom rynku dotyczących jakości produktów i ochrony środowiska. Jednym z głównych kierunków rozwoju jest dalsza automatyzacja procesów produkcyjnych poprzez zastosowanie sztucznej inteligencji i systemów monitorowania opartych na danych analitycznych. Takie podejście pozwoli na jeszcze lepsze dostosowywanie parametrów pracy urządzeń do zmieniających się warunków oraz potrzeb produkcyjnych. Kolejnym istotnym trendem jest rozwój ekologicznych technologii oczyszczania substancji chemicznych, które minimalizują zużycie energii oraz ilość odpadów generowanych podczas procesu destylacji.