Budowa maszyn pneumatycznych opiera się na kilku kluczowych elementach, które współpracują ze sobą w celu zapewnienia efektywnego działania systemu. Na początku warto zwrócić uwagę na sprężarki powietrza, które są sercem każdego systemu pneumatycznego. Ich zadaniem jest sprężanie powietrza i dostarczanie go do układu. Kolejnym istotnym elementem są zbiorniki powietrza, które gromadzą sprężone powietrze, co pozwala na jego późniejsze wykorzystanie w różnych procesach. Również nie można zapomnieć o zaworach, które kontrolują przepływ powietrza w systemie. Zawory te mogą być ręczne lub automatyczne, a ich odpowiedni dobór ma kluczowe znaczenie dla wydajności całego układu. Warto również wspomnieć o siłownikach pneumatycznych, które przekształcają energię sprężonego powietrza w ruch mechaniczny. Dodatkowo, systemy filtracji i osuszania powietrza są niezbędne do zapewnienia czystości i jakości sprężonego powietrza, co wpływa na trwałość i niezawodność maszyn.
Jakie są zastosowania maszyn pneumatycznych w przemyśle
Maszyny pneumatyczne znajdują szerokie zastosowanie w różnych dziedzinach przemysłu, co czyni je niezwykle wszechstronnymi narzędziami. W przemyśle produkcyjnym wykorzystywane są do automatyzacji procesów montażowych oraz pakowania produktów. Dzięki swojej szybkości i precyzji, maszyny te przyczyniają się do zwiększenia wydajności produkcji oraz redukcji kosztów pracy. W branży motoryzacyjnej maszyny pneumatyczne są stosowane do napędu narzędzi takich jak wkrętarki czy młoty udarowe, co umożliwia szybkie i efektywne wykonywanie prac montażowych. W sektorze budowlanym maszyny te znajdują zastosowanie w urządzeniach takich jak betoniarki czy młoty pneumatyczne, które ułatwiają prace budowlane. Ponadto, w przemyśle spożywczym maszyny pneumatyczne są wykorzystywane do transportu surowców oraz pakowania produktów, co zapewnia zachowanie odpowiednich standardów higieny. W medycynie natomiast stosowane są w urządzeniach do wentylacji oraz w sprzęcie chirurgicznym.
Jakie są zalety i wady maszyn pneumatycznych
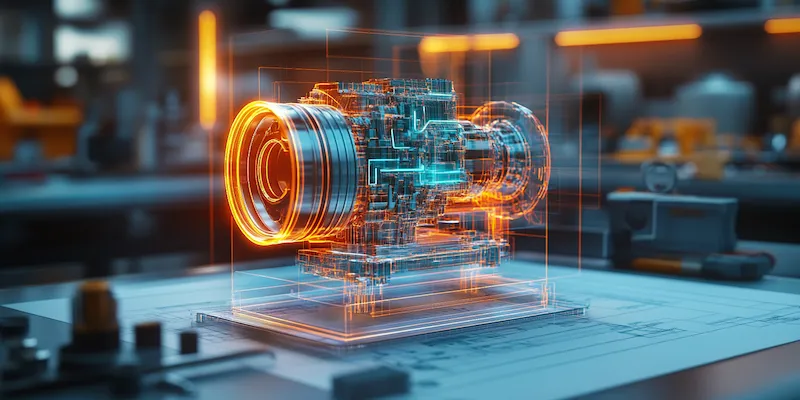
Maszyny pneumatyczne mają wiele zalet, które sprawiają, że są one popularnym wyborem w różnych gałęziach przemysłu. Jedną z głównych korzyści jest ich wysoka wydajność oraz szybkość działania. Sprężone powietrze może być łatwo regulowane i kontrolowane, co pozwala na precyzyjne dostosowanie parametrów pracy maszyny do konkretnego zadania. Dodatkowo maszyny te charakteryzują się prostą budową oraz niskimi kosztami eksploatacyjnymi, ponieważ sprężone powietrze jest powszechnie dostępne i relatywnie tanie. Jednakże istnieją również pewne wady związane z użytkowaniem maszyn pneumatycznych. Przede wszystkim ich wydajność może być ograniczona przez straty ciśnienia w przewodach oraz konieczność regularnej konserwacji systemu filtracji i osuszania powietrza. Ponadto, sprężone powietrze może być mniej efektywne niż inne źródła energii w przypadku długotrwałych operacji wymagających dużej mocy. Warto również zauważyć, że hałas generowany przez niektóre maszyny pneumatyczne może być problemem w środowisku pracy, co wymaga dodatkowych rozwiązań akustycznych.
Jakie są nowoczesne technologie w budowie maszyn pneumatycznych
W ostatnich latach obserwuje się dynamiczny rozwój technologii związanych z budową maszyn pneumatycznych, co przyczynia się do zwiększenia ich efektywności oraz funkcjonalności. Nowoczesne rozwiązania obejmują zastosowanie zaawansowanych materiałów kompozytowych oraz lekkich stopów metali, które pozwalają na redukcję masy urządzeń przy jednoczesnym zachowaniu wysokiej wytrzymałości. Wprowadzenie systemów automatyzacji oraz inteligentnych czujników umożliwia monitorowanie parametrów pracy maszyn w czasie rzeczywistym oraz optymalizację procesów produkcyjnych. Technologie takie jak Internet Rzeczy (IoT) pozwalają na zdalne zarządzanie i diagnostykę systemów pneumatycznych, co znacząco zwiększa ich niezawodność oraz skraca czas przestojów związanych z konserwacją. Dodatkowo rozwój oprogramowania symulacyjnego umożliwia projektowanie bardziej skomplikowanych układów pneumatycznych bez konieczności przeprowadzania kosztownych testów prototypowych.
Jakie są najczęstsze problemy w maszynach pneumatycznych
Maszyny pneumatyczne, mimo swojej niezawodności, mogą napotykać różne problemy, które wpływają na ich wydajność i funkcjonalność. Jednym z najczęstszych problemów jest wyciek sprężonego powietrza, który może prowadzić do znacznych strat energii oraz obniżenia efektywności działania systemu. Wyciek ten może występować w miejscach połączeń przewodów, uszczelek czy zaworów. Regularne kontrole i konserwacja układu pneumatycznego są kluczowe dla minimalizacji tego typu problemów. Innym istotnym zagadnieniem jest zanieczyszczenie sprężonego powietrza, które może prowadzić do uszkodzenia komponentów maszyny oraz obniżenia jakości produkcji. Dlatego tak ważne jest stosowanie odpowiednich filtrów oraz systemów osuszania powietrza. Problemy z ciśnieniem roboczym również mogą wpływać na działanie maszyn pneumatycznych. Zbyt niskie ciśnienie może prowadzić do spadku wydajności, podczas gdy zbyt wysokie może powodować uszkodzenia elementów układu. Warto również zwrócić uwagę na awarie siłowników pneumatycznych, które mogą być spowodowane niewłaściwym doborem komponentów lub ich zużyciem.
Jakie są koszty eksploatacji maszyn pneumatycznych
Koszty eksploatacji maszyn pneumatycznych mogą się znacznie różnić w zależności od wielu czynników, takich jak rodzaj zastosowania, intensywność pracy oraz specyfika używanych komponentów. Na początku warto zwrócić uwagę na koszty związane z energią, ponieważ sprężone powietrze wymaga zasilania sprężarkami, co generuje stałe wydatki na energię elektryczną. W przypadku intensywnego użytkowania maszyn pneumatycznych, te koszty mogą stanowić znaczną część całkowitych wydatków operacyjnych. Kolejnym istotnym elementem są koszty konserwacji i naprawy urządzeń. Regularna kontrola stanu technicznego oraz wymiana zużytych części są niezbędne dla zapewnienia długotrwałej i efektywnej pracy maszyn. Koszty te mogą być zredukowane poprzez odpowiednie planowanie przeglądów oraz stosowanie wysokiej jakości komponentów. Dodatkowo warto uwzględnić koszty związane z zakupem materiałów eksploatacyjnych, takich jak filtry czy oleje do smarowania. Warto również pamiętać o kosztach szkoleń pracowników obsługujących maszyny pneumatyczne, ponieważ ich wiedza i umiejętności mają wpływ na efektywność pracy oraz bezpieczeństwo w miejscu pracy.
Jakie są przyszłościowe kierunki rozwoju technologii pneumatycznej
Przyszłość technologii pneumatycznej zapowiada się bardzo obiecująco, a wiele innowacji ma potencjał do zmiany sposobu, w jaki wykorzystujemy maszyny pneumatyczne w przemyśle. Jednym z kluczowych kierunków rozwoju jest integracja technologii cyfrowych z systemami pneumatycznymi. Dzięki zastosowaniu sztucznej inteligencji oraz analizy danych możliwe będzie optymalizowanie procesów produkcyjnych w czasie rzeczywistym, co przyczyni się do zwiększenia efektywności i redukcji kosztów operacyjnych. Ponadto rozwój Internetu Rzeczy (IoT) umożliwi zdalne monitorowanie stanu maszyn oraz przewidywanie awarii zanim one wystąpią, co pozwoli na szybszą reakcję i minimalizację przestojów. Innowacyjne materiały kompozytowe oraz technologie druku 3D otwierają nowe możliwości w projektowaniu komponentów pneumatycznych, co może prowadzić do lżejszych i bardziej wytrzymałych konstrukcji. Również ekologiczne podejście do produkcji sprawia, że coraz więcej firm poszukuje rozwiązań zmniejszających zużycie energii oraz emisję gazów cieplarnianych związanych z działaniem systemów pneumatycznych. Wprowadzenie bardziej efektywnych sprężarek oraz systemów recyklingu sprężonego powietrza to tylko niektóre z przykładów działań podejmowanych w tym kierunku.
Jakie są różnice między systemami pneumatycznymi a hydraulicznymi
Systemy pneumatyczne i hydrauliczne to dwa różne podejścia do przenoszenia energii mechanicznej, które mają swoje unikalne cechy i zastosowania. Główna różnica między nimi polega na medium roboczym: systemy pneumatyczne wykorzystują sprężone powietrze jako nośnik energii, podczas gdy systemy hydrauliczne opierają się na cieczy hydraulicznej. Ta fundamentalna różnica wpływa na wiele aspektów ich działania oraz zastosowania. Systemy pneumatyczne charakteryzują się większą szybkością reakcji i prostszą budową, co czyni je idealnymi do zastosowań wymagających dynamicznych ruchów oraz precyzyjnego sterowania. Z drugiej strony systemy hydrauliczne oferują znacznie większą moc i moment obrotowy przy mniejszych rozmiarach urządzeń, co sprawia, że są preferowane w aplikacjach wymagających dużych sił, takich jak prasy czy maszyny budowlane. Dodatkowo systemy hydrauliczne są mniej podatne na straty ciśnienia niż systemy pneumatyczne, co czyni je bardziej efektywnymi w długich układach rurociągowych. Jednakże systemy hydrauliczne wymagają bardziej skomplikowanej konserwacji ze względu na ryzyko wycieków cieczy oraz konieczność stosowania filtracji cieczy roboczej.
Jakie są kluczowe czynniki wpływające na wybór maszyn pneumatycznych
Wybór odpowiednich maszyn pneumatycznych do konkretnego zastosowania jest kluczowy dla osiągnięcia optymalnej wydajności i efektywności produkcji. Istnieje wiele czynników, które należy wziąć pod uwagę przy podejmowaniu decyzji o zakupie lub modernizacji sprzętu pneumatycznego. Przede wszystkim należy określić wymagania dotyczące mocy i wydajności maszyny w kontekście planowanych procesów produkcyjnych. Ważne jest również zwrócenie uwagi na rodzaj materiału, który będzie przetwarzany lub transportowany za pomocą maszyny pneumatycznej, ponieważ różne materiały mogą wymagać różnych parametrów pracy urządzenia. Kolejnym czynnikiem jest dostępność serwisu oraz wsparcia technicznego producenta lub dostawcy sprzętu; szybka reakcja w przypadku awarii jest kluczowa dla minimalizacji przestojów produkcyjnych. Należy także rozważyć kwestie związane z kosztami eksploatacyjnymi oraz konserwacyjnymi; wybór tańszych komponentów może prowadzić do wyższych kosztów w dłuższej perspektywie czasowej ze względu na konieczność częstych napraw czy wymiany części.