Kompresor to urządzenie mechaniczne, którego głównym zadaniem jest zwiększenie ciśnienia gazu poprzez zmniejszenie jego objętości. W praktyce oznacza to, że kompresory są wykorzystywane w różnych dziedzinach przemysłu oraz w codziennym życiu, na przykład w klimatyzacji, chłodnictwie czy w narzędziach pneumatycznych. Działanie kompresora opiera się na zasadzie sprężania gazu, co prowadzi do wzrostu jego ciśnienia. W zależności od konstrukcji i zastosowania, kompresory mogą działać na różnych zasadach, takich jak sprężanie dynamiczne lub statyczne. W przypadku kompresorów dynamicznych, takich jak sprężarki odśrodkowe, gaz jest sprężany przez wirnik, który nadaje mu prędkość. Natomiast w kompresorach statycznych, takich jak tłokowe, gaz jest sprężany przez ruch tłoka w cylindrze.
Jakie są rodzaje kompresorów i ich zastosowania?
Wyróżniamy kilka podstawowych typów kompresorów, które różnią się zarówno budową, jak i przeznaczeniem. Najpopularniejsze z nich to kompresory tłokowe, śrubowe oraz spiralne. Kompresory tłokowe charakteryzują się prostą konstrukcją i są często stosowane w małych warsztatach oraz domowych zastosowaniach. Ich działanie polega na ruchu tłoka w cylindrze, co powoduje sprężanie powietrza. Kompresory śrubowe natomiast są bardziej zaawansowane technologicznie i znajdują zastosowanie w przemyśle ciężkim, gdzie wymagane są duże ilości sprężonego powietrza. Dzięki swojej wydajności i niezawodności są idealnym rozwiązaniem dla zakładów produkcyjnych. Kompresory spiralne to kolejny typ urządzeń, które wykorzystują spiralne wirniki do sprężania gazu. Są one ciche i efektywne, co sprawia, że znajdują zastosowanie w systemach klimatyzacyjnych oraz chłodniczych.
Jakie są kluczowe zalety korzystania z kompresorów?
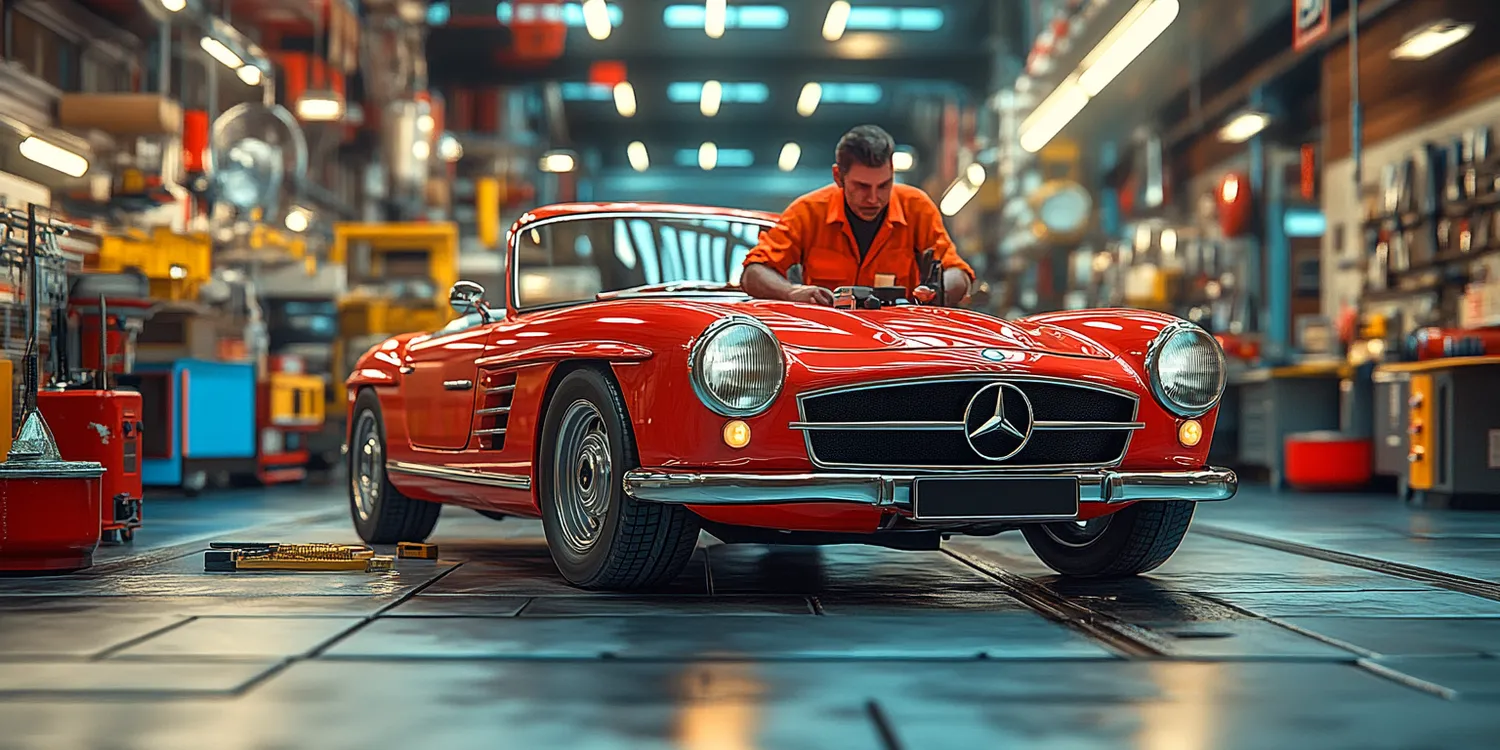
Korzystanie z kompresorów niesie ze sobą wiele korzyści zarówno dla przemysłu, jak i dla użytkowników indywidualnych. Przede wszystkim kompresory umożliwiają efektywne wykorzystanie energii poprzez sprężanie gazu, co pozwala na oszczędność kosztów eksploatacyjnych. Dzięki nim można uzyskać wysokie ciśnienie powietrza potrzebne do zasilania narzędzi pneumatycznych czy systemów klimatyzacyjnych. Kolejną zaletą jest ich wszechstronność – kompresory mogą być stosowane w różnych branżach, od budownictwa po medycynę. Umożliwiają one także automatyzację procesów produkcyjnych oraz poprawiają komfort pracy poprzez dostarczanie sprężonego powietrza do różnych urządzeń. Dodatkowo nowoczesne kompresory są coraz bardziej energooszczędne i przyjazne dla środowiska, co staje się istotnym czynnikiem w dobie rosnącej świadomości ekologicznej.
Jakie czynniki należy uwzględnić przy wyborze kompresora?
Wybór odpowiedniego kompresora to kluczowy element zapewniający jego efektywność oraz długowieczność. Przy podejmowaniu decyzji warto zwrócić uwagę na kilka istotnych czynników. Po pierwsze należy określić wymagania dotyczące wydajności – czyli ilości sprężonego powietrza potrzebnego do realizacji konkretnych zadań. Ważne jest również ciśnienie robocze, które powinno być dostosowane do specyfiki używanych narzędzi pneumatycznych czy systemów klimatyzacyjnych. Kolejnym aspektem jest rodzaj zasilania – dostępność energii elektrycznej lub innego źródła napędu może wpłynąć na wybór konkretnego modelu. Należy także rozważyć mobilność urządzenia; jeśli planujemy używać kompresora w różnych lokalizacjach, warto postawić na model przenośny lub o niewielkich wymiarach. Ostatnim czynnikiem jest budżet – ceny kompresorów mogą się znacznie różnić w zależności od ich typu i parametrów technicznych.
Jakie są najczęstsze problemy z kompresorami i ich rozwiązania?
Kompresory, jak każde inne urządzenia mechaniczne, mogą napotykać różne problemy w trakcie eksploatacji. Jednym z najczęstszych problemów jest nadmierne nagrzewanie się urządzenia, co może prowadzić do jego uszkodzenia. Przyczyną tego zjawiska może być niewłaściwe smarowanie lub zbyt mała ilość powietrza w układzie. Aby temu zapobiec, warto regularnie kontrolować poziom oleju oraz dbać o odpowiednią wentylację wokół kompresora. Innym częstym problemem jest wyciek powietrza, który może występować na skutek uszkodzeń uszczelek lub połączeń. W takim przypadku konieczne jest przeprowadzenie dokładnej inspekcji i wymiana uszkodzonych elementów. Zdarza się również, że kompresor nie osiąga wymaganego ciśnienia roboczego, co może być spowodowane zanieczyszczeniem filtrów powietrza lub niewłaściwą regulacją ciśnienia. Regularna konserwacja oraz czyszczenie filtrów pomogą utrzymać urządzenie w dobrym stanie.
Jakie są koszty zakupu i eksploatacji kompresora?
Zakup kompresora wiąże się z różnymi kosztami, które mogą się znacznie różnić w zależności od typu urządzenia oraz jego parametrów technicznych. Ceny kompresorów tłokowych zaczynają się od kilkuset złotych za modele przeznaczone do użytku domowego, natomiast bardziej zaawansowane kompresory śrubowe mogą kosztować kilka tysięcy złotych. Warto również uwzględnić dodatkowe wydatki związane z akcesoriami, takimi jak węże, złączki czy filtry powietrza. Koszty eksploatacji kompresora obejmują przede wszystkim zużycie energii elektrycznej oraz regularne serwisowanie urządzenia. Wydajność energetyczna kompresora ma kluczowe znaczenie dla obniżenia kosztów eksploatacyjnych; nowoczesne modele często charakteryzują się lepszymi parametrami energetycznymi niż starsze wersje. Dodatkowo warto pamiętać o kosztach związanych z wymianą oleju oraz filtrów, które powinny być przeprowadzane zgodnie z zaleceniami producenta.
Jakie są innowacje technologiczne w dziedzinie kompresorów?
W ostatnich latach branża kompresorów przechodzi dynamiczny rozwój dzięki postępom technologicznym. Producenci wprowadzają innowacyjne rozwiązania mające na celu zwiększenie efektywności energetycznej oraz poprawę wydajności urządzeń. Jednym z takich rozwiązań są kompresory bezolejowe, które eliminują potrzebę stosowania oleju do smarowania, co przekłada się na mniejsze koszty eksploatacji oraz ograniczenie wpływu na środowisko. Kolejnym trendem jest automatyzacja procesów związanych z obsługą kompresorów; nowoczesne modele często wyposażone są w systemy monitorujące parametry pracy oraz automatyczne wyłączniki, które zapobiegają przeciążeniu urządzenia. Wprowadzenie technologii IoT (Internet of Things) pozwala na zdalne monitorowanie stanu kompresora oraz jego parametrów pracy, co umożliwia szybsze reagowanie na ewentualne problemy. Dodatkowo coraz więcej producentów stawia na energooszczędność swoich produktów, co jest odpowiedzią na rosnącą świadomość ekologiczną użytkowników oraz regulacje prawne dotyczące emisji CO2.
Jak dbać o kompresor, aby służył przez długi czas?
Aby zapewnić długowieczność i niezawodność działania kompresora, niezwykle istotna jest regularna konserwacja oraz właściwe użytkowanie urządzenia. Przede wszystkim należy przestrzegać zaleceń producenta dotyczących serwisowania i wymiany filtrów powietrza oraz oleju. Regularne czyszczenie filtrów pozwoli na utrzymanie optymalnego przepływu powietrza i zapobiegnie przegrzewaniu się silnika. Ważnym aspektem jest także kontrola poziomu oleju; niewłaściwy poziom może prowadzić do uszkodzeń mechanicznych oraz skrócenia żywotności urządzenia. Należy również zwrócić uwagę na stan uszczelek i połączeń – ich regularna inspekcja pozwoli na szybkie wykrycie ewentualnych wycieków powietrza. Oprócz tego warto zadbać o odpowiednią wentylację wokół kompresora, aby uniknąć przegrzewania się urządzenia podczas pracy. Użytkownicy powinni także unikać przeciążania kompresora poprzez dostosowanie jego pracy do specyfiki używanych narzędzi pneumatycznych czy systemów klimatyzacyjnych.
Jakie są zastosowania kompresorów w różnych branżach przemysłowych?
Kompresory znajdują szerokie zastosowanie w wielu branżach przemysłowych, co czyni je niezwykle wszechstronnymi narzędziami. W przemyśle budowlanym sprężone powietrze wykorzystywane jest do zasilania narzędzi pneumatycznych takich jak młoty udarowe czy wkrętarki, co znacznie zwiększa efektywność pracy ekip budowlanych. W branży motoryzacyjnej kompresory służą do lakierowania pojazdów oraz jako źródło sprężonego powietrza do testowania układów pneumatycznych w samochodach. W przemyśle spożywczym sprężone powietrze jest wykorzystywane do pakowania produktów oraz transportu materiałów sypkich w procesach produkcyjnych. Kompresory znajdują także zastosowanie w medycynie; sprężone powietrze jest niezbędne w aparatach do wentylacji mechanicznej czy systemach dostarczania tlenu pacjentom. W sektorze chłodnictwa i klimatyzacji sprężarki są kluczowym elementem systemów chłodniczych, gdzie odpowiadają za cykl sprężania czynnika chłodniczego.
Jakie są przyszłe kierunki rozwoju technologii kompresorowej?
Przyszłość technologii kompresorowej zapowiada się obiecująco dzięki ciągłemu rozwojowi innowacyjnych rozwiązań oraz rosnącej świadomości ekologicznej użytkowników. Producenci będą koncentrować się na tworzeniu coraz bardziej energooszczędnych modeli, które będą spełniały rygorystyczne normy emisji CO2 i innych substancji szkodliwych dla środowiska. Rozwój technologii bezolejowych będzie kontynuowany, co przyczyni się do zmniejszenia wpływu na środowisko naturalne oraz obniżenia kosztów eksploatacji urządzeń. Wprowadzenie zaawansowanych systemów monitorujących pozwoli na lepszą kontrolę parametrów pracy kompresorów oraz szybsze diagnozowanie ewentualnych usterek. Coraz większą rolę będą odgrywać także rozwiązania związane z automatyzacją procesów przemysłowych; inteligentne systemy zarządzania będą mogły dostosowywać pracę kompresora do aktualnych potrzeb produkcyjnych w czasie rzeczywistym.