Budowa maszyn to złożony proces, który wymaga starannego planowania oraz zastosowania odpowiednich technologii. Kluczowe etapy tego procesu obejmują analizę wymagań, projektowanie koncepcyjne, szczegółowe projektowanie oraz testowanie. Na początku inżynierowie muszą dokładnie zrozumieć potrzeby klienta i specyfikacje techniczne, co pozwala na stworzenie wstępnych założeń dotyczących maszyny. Następnie przechodzi się do fazy projektowania koncepcyjnego, gdzie tworzy się ogólny zarys konstrukcji oraz wybiera odpowiednie materiały i technologie produkcji. W tej fazie istotne jest również uwzględnienie aspektów ergonomicznych oraz bezpieczeństwa użytkowania. Kolejnym krokiem jest szczegółowe projektowanie, które obejmuje tworzenie rysunków technicznych, schematów oraz modeli 3D. W końcu, po zakończeniu procesu projektowania, maszyna przechodzi przez fazę testowania, gdzie sprawdzana jest jej funkcjonalność oraz wydajność.
Jakie technologie są stosowane w budowie maszyn
W dzisiejszych czasach budowa maszyn opiera się na zaawansowanych technologiach, które znacznie ułatwiają proces projektowania i produkcji. Wśród najpopularniejszych technologii można wymienić modelowanie 3D, symulacje komputerowe oraz druk 3D. Modelowanie 3D pozwala inżynierom na wizualizację projektu w trzech wymiarach, co ułatwia identyfikację potencjalnych problemów jeszcze przed rozpoczęciem produkcji. Symulacje komputerowe umożliwiają testowanie różnych scenariuszy działania maszyny w wirtualnym środowisku, co pozwala na optymalizację jej parametrów. Druk 3D z kolei staje się coraz bardziej popularny w prototypowaniu części maszyn, ponieważ pozwala na szybkie i tanie wytwarzanie skomplikowanych kształtów. Dodatkowo, technologie takie jak CAD (Computer-Aided Design) i CAM (Computer-Aided Manufacturing) wspierają inżynierów w procesie projektowania i produkcji, automatyzując wiele zadań i zwiększając dokładność wykonania.
Jakie umiejętności są potrzebne do projektowania maszyn
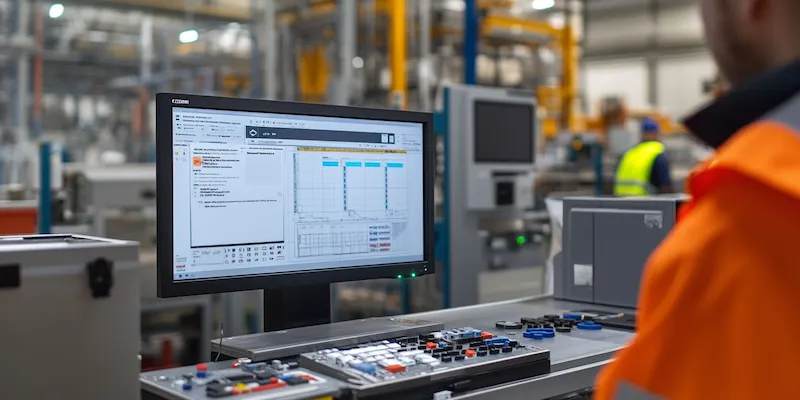
Aby skutecznie zajmować się budową maszyn i ich projektowaniem, inżynierowie muszą posiadać szereg umiejętności technicznych oraz interpersonalnych. Przede wszystkim niezbędna jest znajomość zasad mechaniki oraz materiałoznawstwa, co pozwala na dobór odpowiednich komponentów do konstrukcji maszyny. Umiejętność posługiwania się oprogramowaniem CAD jest również kluczowa, ponieważ większość współczesnych projektów realizowana jest przy użyciu takich narzędzi. Ponadto inżynierowie powinni być zaznajomieni z metodami analizy wytrzymałościowej oraz symulacji komputerowych, co pozwala na przewidywanie zachowań maszyny pod różnymi obciążeniami. Oprócz umiejętności technicznych ważne są także kompetencje miękkie, takie jak zdolności komunikacyjne i umiejętność pracy zespołowej. Budowa maszyn często wymaga współpracy z innymi specjalistami, dlatego umiejętność efektywnej komunikacji jest niezbędna do osiągnięcia wspólnych celów.
Jakie są najczęstsze wyzwania w budowie maszyn
Budowa maszyn wiąże się z wieloma wyzwaniami, które mogą wpłynąć na jakość finalnego produktu oraz czas realizacji projektu. Jednym z najczęstszych problemów jest konieczność dostosowania projektu do zmieniających się wymagań klientów lub norm prawnych. W miarę postępu technologicznego pojawiają się nowe standardy dotyczące bezpieczeństwa czy efektywności energetycznej, co może wymusić modyfikacje już zaplanowanych rozwiązań. Kolejnym wyzwaniem jest zarządzanie kosztami produkcji; inżynierowie muszą znaleźć równowagę między jakością a ceną używanych materiałów oraz technologii. Problemy mogą także wystąpić podczas fazy testowania maszyny; wykrycie błędów konstrukcyjnych lub funkcjonalnych może prowadzić do opóźnień w harmonogramie prac. Dodatkowo globalizacja rynku sprawia, że konkurencja staje się coraz większa, co wymusza na firmach ciągłe doskonalenie swoich produktów oraz procesów produkcyjnych.
Jakie są najnowsze trendy w projektowaniu maszyn
W ostatnich latach w budowie maszyn można zaobserwować wiele interesujących trendów, które mają na celu zwiększenie efektywności oraz zrównoważonego rozwoju. Jednym z najważniejszych kierunków jest automatyzacja procesów produkcyjnych. Dzięki zastosowaniu robotów przemysłowych oraz systemów automatycznego sterowania, firmy mogą znacznie zwiększyć wydajność produkcji oraz ograniczyć błędy ludzkie. Kolejnym istotnym trendem jest integracja Internetu Rzeczy (IoT) w maszynach, co pozwala na zbieranie danych w czasie rzeczywistym oraz ich analizę. Dzięki temu inżynierowie mogą monitorować wydajność maszyn, przewidywać awarie i optymalizować procesy produkcyjne. Zrównoważony rozwój staje się również kluczowym aspektem projektowania maszyn; coraz więcej firm stawia na ekologiczne materiały oraz technologie, które minimalizują negatywny wpływ na środowisko. W kontekście zmieniających się potrzeb rynku, projektowanie modułowe zyskuje na popularności, co pozwala na łatwiejsze dostosowywanie maszyn do specyficznych wymagań klientów.
Jakie są podstawowe zasady ergonomii w budowie maszyn
Ergonomia odgrywa kluczową rolę w projektowaniu maszyn, ponieważ ma bezpośredni wpływ na komfort i bezpieczeństwo użytkowników. Podstawowe zasady ergonomii obejmują dostosowanie maszyny do potrzeb i możliwości człowieka, co pozwala na zmniejszenie ryzyka urazów oraz poprawę wydajności pracy. Kluczowym elementem jest analiza stanowiska pracy; inżynierowie powinni zwrócić uwagę na wysokość, kąt nachylenia oraz dostępność wszystkich niezbędnych narzędzi i komponentów. Ważne jest również uwzględnienie aspektów wizualnych, takich jak oświetlenie czy kontrast kolorystyczny, które mogą wpływać na komfort pracy. Dodatkowo, projektując maszyny, należy brać pod uwagę różnorodność użytkowników; różnice w wzroście, sile czy umiejętnościach manualnych powinny być uwzględnione w procesie projektowania. Ergonomiczne uchwyty, intuicyjne panele sterujące oraz odpowiednie rozmieszczenie elementów to tylko niektóre z rozwiązań, które mogą znacząco poprawić komfort użytkowania maszyny.
Jakie są kluczowe aspekty bezpieczeństwa w budowie maszyn
Bezpieczeństwo jest jednym z najważniejszych aspektów przy projektowaniu i budowie maszyn. Inżynierowie muszą przestrzegać rygorystycznych norm oraz przepisów dotyczących bezpieczeństwa, aby zminimalizować ryzyko wypadków i urazów. Kluczowym krokiem jest przeprowadzenie analizy ryzyka, która pozwala zidentyfikować potencjalne zagrożenia związane z użytkowaniem maszyny. Na podstawie tej analizy można wdrożyć odpowiednie środki ochrony, takie jak osłony mechaniczne czy systemy awaryjnego zatrzymania. Warto również zadbać o ergonomiczne rozwiązania, które ułatwiają obsługę maszyny i zmniejszają ryzyko kontuzji. Szkolenie pracowników w zakresie obsługi maszyn oraz procedur bezpieczeństwa jest równie istotne; dobrze przeszkolony personel potrafi skutecznie reagować w sytuacjach awaryjnych i unikać niebezpiecznych zachowań. Regularne przeglądy techniczne oraz konserwacja maszyn są kolejnymi ważnymi elementami zapewniającymi bezpieczeństwo ich użytkowania.
Jakie są metody testowania maszyn po ich budowie
Testowanie maszyn po ich budowie jest kluczowym etapem zapewniającym ich prawidłowe działanie oraz spełnienie określonych norm jakościowych. Proces ten zazwyczaj rozpoczyna się od testów funkcjonalnych, które mają na celu sprawdzenie wszystkich funkcji maszyny zgodnie z jej specyfikacją techniczną. Inżynierowie przeprowadzają różnorodne testy obciążeniowe, aby ocenić wydajność maszyny pod różnymi warunkami pracy. Testy te pozwalają na identyfikację ewentualnych słabości konstrukcji oraz umożliwiają dokonanie niezbędnych poprawek przed rozpoczęciem produkcji seryjnej. Kolejnym istotnym krokiem jest testowanie bezpieczeństwa; inżynierowie muszą upewnić się, że wszystkie systemy zabezpieczeń działają prawidłowo i że maszyna spełnia obowiązujące normy bezpieczeństwa. Po zakończeniu testów funkcjonalnych i bezpieczeństwa przeprowadza się również testy długoterminowe, które mają na celu ocenę trwałości maszyny w czasie rzeczywistym użytkowania.
Jakie są wyzwania związane z prototypowaniem maszyn
Prototypowanie maszyn to kluczowy etap w procesie ich budowy, jednak wiąże się z wieloma wyzwaniami, które mogą wpłynąć na czas realizacji projektu oraz jego koszty. Jednym z głównych problemów jest konieczność szybkiego dostosowywania prototypu do zmieniających się wymagań klientów lub nowych technologii. Często zdarza się również, że podczas prototypowania pojawiają się nieprzewidziane trudności związane z materiałami lub technologią produkcji, co może prowadzić do opóźnień i dodatkowych kosztów. Kolejnym wyzwaniem jest znalezienie równowagi między jakością a ceną; inżynierowie muszą podejmować decyzje dotyczące wyboru materiałów oraz technologii produkcji tak, aby prototyp był zarówno funkcjonalny, jak i ekonomiczny. Dodatkowo współpraca między różnymi zespołami – inżynieryjnymi, marketingowymi czy sprzedażowymi – może być skomplikowana i wymagać dużej koordynacji działań.
Jakie są korzyści płynące z zastosowania symulacji komputerowych
Symulacje komputerowe stały się nieodłącznym elementem procesu projektowania i budowy maszyn dzięki swoim licznym zaletom. Przede wszystkim umożliwiają one przewidywanie zachowań maszyny pod różnymi warunkami eksploatacyjnymi jeszcze przed jej fizycznym wykonaniem. Dzięki temu inżynierowie mogą szybko identyfikować potencjalne problemy i optymalizować konstrukcję bez ponoszenia wysokich kosztów związanych z prototypowaniem czy modyfikacjami fizycznymi. Symulacje pozwalają także na przeprowadzanie testów obciążeniowych oraz analizy wytrzymałościowej w warunkach laboratoryjnych, co zwiększa dokładność wyników i pozwala na lepsze dopasowanie projektu do wymagań klienta. Dodatkowo wykorzystanie symulacji komputerowych przyspiesza proces projektowania; inżynierowie mogą eksperymentować z różnymi rozwiązaniami bez potrzeby angażowania dużych zasobów materiałowych czy czasowych.